Other Refrigeration Systems
Compressors in refrigeration
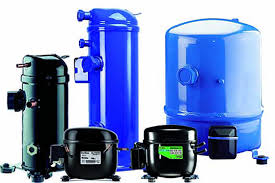

Finstar Industrial Systems’ compressors are the key components that power refrigeration systems by continuously circulating refrigerant to enable effective cooling. Our wide range of refrigeration compressors in Nairobi Kenya, is designed to provide reliable performance, energy efficiency and versatility for different applications from small cold rooms to large industrial cooling facilities.
Key features of refrigeration compressors
- Different types of refrigeration compressors: reciprocating, scroll, screw, centrifugal
- High energy efficiency ratings to reduce operating costs
- Strong construction for long-lasting use in tough environments
- Suitable for various cooling capacities and temperatures in Nairobi
- Customizable options to meet your specific application requirements
- Easy to install and access for maintenance
- Backed by Finstar’s proven expertise in refrigeration solutions in Kenya.
Functions of a Compressor in Refrigeration systems
- Compressing Refrigerant: Converts low-pressure, low-temperature refrigerant gas from the evaporator into a high-pressure, high-temperature gas.
- Circulating Refrigerant: Ensures continuous movement of the refrigerant through the system, driving the refrigeration cycle.
- Heat Exchange: Facilitates the release of absorbed heat from the refrigerant in the condenser, enabling the cooling process in the evaporator.
Types of Refrigeration Compressors
-
Reciprocating Compressors:
- Mechanism: Use a piston driven by a crankshaft to compress the refrigerant.
- Applications: Widely used in domestic refrigerators, air conditioners, and small commercial systems.
- Advantages: Durable, capable of high-pressure ratios.
-
Rotary Compressors:
- Mechanism: Use a rotating mechanism, often with a rolling piston or vane, to compress the refrigerant.
- Applications: Common in window air conditioners and small split systems.
- Advantages: Compact, quiet operation, efficient.
-
Scroll Compressors:
- Mechanism: Utilize two interleaved spiral scrolls, one stationary and one moving, to compress the refrigerant.
- Applications: Common in residential and light commercial air conditioning and refrigeration.
- Advantages: High efficiency, quiet, fewer moving parts, reliable.
-
Screw Compressors:
- Mechanism: Employ two helical rotors that rotate and compress the refrigerant.
- Applications: Large commercial and industrial refrigeration systems.
- Advantages: High efficiency, continuous operation, suitable for large capacities.
-
Centrifugal Compressors:
- Mechanism: Use a rotating impeller to increase the velocity of the refrigerant, converting it to pressure.
- Applications: Large-scale industrial and commercial systems.
- Advantages: High efficiency at large capacities, smooth operation.
Selecting the Right Compressor
- Capacity Requirements: Match the compressor size to the cooling load of the application.
- Refrigerant Compatibility: Ensure the compressor is compatible with the type of refrigerant used.
- Efficiency: Consider the energy efficiency of the compressor, particularly for long-term operating costs.
- Noise Level: Evaluate the noise output, especially for residential or commercial applications where quiet operation is crucial.
- Maintenance Needs: Factor in the maintenance requirements and ease of serviceability.
Maintenance of Refrigeration Compressors
- Regular Inspections: Check for signs of wear, leaks, and proper operation. Inspect belts, electrical connections, and mounting hardware.
- Lubrication: Ensure the compressor is adequately lubricated according to the manufacturer’s specifications. Replace or replenish oil as needed.
- Cleaning: Keep the compressor and surrounding areas clean to prevent dust and debris from affecting operation. Clean or replace air filters regularly.
- Refrigerant Levels: Maintain correct refrigerant levels to ensure efficient operation. Check for leaks and repair them promptly.
- Operating Conditions: Monitor temperature and pressure levels to ensure they are within acceptable ranges. Address any deviations immediately.
- Vibration Checks: Ensure the compressor is securely mounted and check for any abnormal vibrations, which could indicate misalignment or other issues.
Refrigeration condensors
Condensers are critical components in refrigeration systems, responsible for dissipating heat from the high-pressure, hot refrigerant vapor. At Finstar Industrial in we offer a comprehensive range of high-quality refrigeration condensers designed to ensure efficient heat transfer and optimal system performance.
Key features of Refrigeration condensers
- Various condenser types: air-cooled, water-cooled, evaporative, plate and shell
- Efficient heat transfer for optimal system performance
- Durable construction for long-lasting operation
- Easy installation and maintenance access
- Customizable solutions to meet specific application requirements
- Backed by Finstar’s expertise in refrigeration solutions in Kenya
Functions of Refrigeration Condensers
- Heat Rejection: Transfer heat absorbed by the refrigerant in the evaporator to the surroundings.
- Condensation: Convert high-pressure, high-temperature refrigerant vapor into a liquid state.
- Pressure Reduction: Lower the pressure of the refrigerant, preparing it for expansion in the expansion valve or metering device.
- Maintain Refrigerant Flow: Ensure proper circulation of refrigerant through the system by providing a controlled environment for condensation.
Types of Refrigeration Condensers
Our condensers are available in various types to suit different applications and cooling requirements:
Air-Cooled Condensers:
- Working Principle: Use ambient air to remove heat from the refrigerant.
- Applications: Commonly used in small to medium-sized refrigeration systems, including residential and commercial refrigerators, freezers, and air conditioning units.
- Advantages: Simple design, no requirement for water supply, suitable for indoor and outdoor installations.
Water-Cooled Condensers:
- Working Principle: Utilize water as the cooling medium to remove heat from the refrigerant.
- Applications: Ideal for high-capacity refrigeration systems and industrial applications where air-cooled condensers are impractical or insufficient.
- Advantages: Greater efficiency compared to air-cooled condensers, unaffected by ambient temperature variations.
Evaporative Condensers:
- Working Principle: Combine elements of air and water-cooled condensers by using water evaporation to remove heat from the refrigerant.
- Applications: Common in large-scale industrial refrigeration systems, such as cold storage warehouses, food processing plants, and HVAC systems.
- Advantages: High efficiency, particularly in hot climates, compact design, reduced water consumption compared to water-cooled condensers.
Shell and Tube Condensers:
- Construction: Consist of a series of tubes enclosed within a shell through which the refrigerant flows, with water or air circulating around the tubes to remove heat.
- Applications: Used in various refrigeration and air conditioning systems, especially those requiring high heat transfer rates and durability.
- Advantages: Efficient heat transfer, suitable for high-pressure and high-temperature applications, easy to clean and maintain.
Maintenance of Refrigeration Condensers
- Cleaning: Regularly clean the condenser coils or tubes to remove dust, dirt, and debris that can inhibit heat transfer.
- Inspection: Periodically inspect the condenser for signs of corrosion, leaks, or damage. Address any issues promptly to prevent further damage.
- Refrigerant Charge: Ensure the refrigerant charge is correct and adjust if necessary to optimize performance.
- Water Treatment: If using water-cooled or evaporative condensers, implement water treatment measures to prevent scaling, fouling, and corrosion.
- Airflow: Ensure proper airflow around air-cooled condensers by maintaining adequate clearance and removing obstructions.
- Controls and Safety Devices: Regularly check and calibrate control settings and safety devices to ensure proper operation and protect against overheating or system failures.
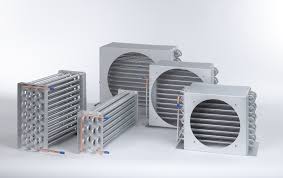
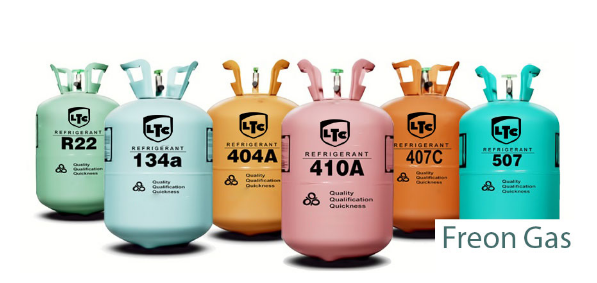
Freon Gas for refrigeration
Freon gases, also known as refrigerants, are essential components in refrigeration systems, enabling the transfer of heat and providing cooling effects. At Finstar Industrial we offer a wide range of Freon gases suitable for various refrigeration applications, from residential air conditioners to commercial and industrial cooling systems.
Our Freon gas products come in different types, each designed to meet specific cooling requirements and environmental regulations. Some of the common types we offer include:
- R-22 (HCFC-22): A widely used refrigerant in older systems, though being phased out due to its ozone-depleting potential.
- R-134a (HFC-134a): A popular alternative to R-22, commonly used in automotive air conditioning and household refrigerators.
- R-404A (HFC Blend): A blend of refrigerants suitable for commercial refrigeration systems, such as those used in supermarkets and food storage facilities.
- R-410A (HFC Blend): A high-performance refrigerant used in modern air conditioning systems, offering improved energy efficiency.
- R-600a (Isobutane): A hydrocarbon refrigerant used in some household refrigerators and freezers, known for its low environmental impact.
At Finstar, we ensure that our Freon gases are of the highest quality, meeting industry standards and environmental regulations. Our experienced technicians can assist you in selecting the most appropriate refrigerant for your specific application, ensuring optimal performance and energy efficiency.
Key features of Freon Gases
- Wide range of Freon gas types for various refrigeration applications
- Compatible with different refrigeration systems and cooling capacities
- High-quality products meeting industry standards and environmental regulations
- Expert guidance in selecting the appropriate refrigerant
- Backed by Finstar’s expertise in refrigeration solutions in Kenya
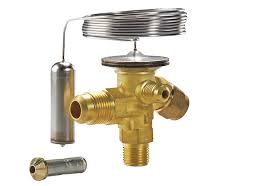
Expansion valves
Expansion valves are crucial components in refrigeration systems, regulating the flow of liquid refrigerant into the evaporator and facilitating the phase change from liquid to vapor, enabling the cooling process. At Finstar Industrial Systems in Nairobi, Kenya, we offer a wide range of high-quality expansion valves designed to ensure precise control and efficient operation of your refrigeration systems.
Key features of Expansion valves
- Various expansion valve types: Thermostatic, Electronic, Constant Pressure, Automatic
- Precise refrigerant flow control for efficient cooling
- Durable construction for long-lasting performance
- Easy installation and maintenance access
- Customizable solutions to meet specific application requirements
- Backed by Finstar’s expertise in refrigeration solutions in Kenya.
Functions of Expansion Valves
- Refrigerant Flow Control: Regulate the flow of refrigerant into the evaporator coil based on system demand.
- Pressure Regulation: Maintain a specific pressure drop across the expansion valve to ensure proper operation of the refrigeration cycle.
- Superheat Control: Adjust the superheat of the refrigerant leaving the evaporator coil to optimize system efficiency and performance.
Types of Expansion Valves
Thermal Expansion Valve (TXV):
- Working Principle: Uses a thermal sensing element (bulb) connected to the suction line to detect evaporator coil temperature. The bulb senses the temperature and modulates the valve opening to maintain a constant superheat.
- Applications: Commonly used in air conditioning and refrigeration systems where precise superheat control is required.
- Advantages: Provides accurate and stable superheat control over a wide range of operating conditions.
Electronic Expansion Valve (EEV):
- Working Principle: Utilizes electronic sensors and a stepper motor to control the valve opening based on real-time system parameters, such as evaporator temperature, pressure, and superheat.
- Applications: Used in advanced refrigeration and air conditioning systems, including variable refrigerant flow (VRF) systems and precision cooling applications.
- Advantages: Offers precise control of refrigerant flow and superheat, adaptable to changing load conditions, and compatible with advanced control strategies.
Automatic Expansion Valve (AEV):
- Working Principle: Operates based on a combination of pressure and temperature to regulate refrigerant flow into the evaporator. The valve opening adjusts automatically in response to changes in system conditions.
- Applications: Found in some refrigeration systems where precise superheat control is not critical, such as low-temperature applications or systems with relatively constant loads.
- Advantages: Simple design, reliable operation, suitable for applications with stable operating conditions.
Maintenance of Expansion Valves
- Regular Inspection: Check expansion valves for signs of leaks, corrosion, or mechanical damage.
- Superheat Adjustment: Periodically adjust the superheat setting of thermal expansion valves to optimize system performance.
- Cleaning: Keep the valve and surrounding components clean to prevent debris buildup or fouling that can affect valve operation.
- Temperature Calibration: Calibrate temperature sensors and thermal bulbs to ensure accurate temperature sensing and superheat control.
- Pressure Testing: Conduct pressure testing to verify proper valve operation and refrigerant flow control.
- Replacement of Faulty Components: Replace any faulty components, such as sensors, bulbs, or valve assemblies, as needed to maintain optimal performance.
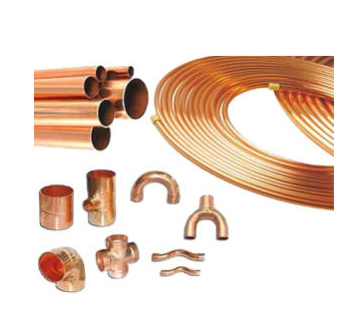
Refrigeration copper pipes
Copper pipes are an essential component in refrigeration systems, serving as the conduits for the refrigerant to flow through the various components. At Finstar Industrial Systems in Nairobi, Kenya, we offer a comprehensive range of high-quality refrigeration copper pipes designed to meet the demanding requirements of various cooling applications.
Key features of Refrigeration copper pipes
- Different types: Soft, Hard, ACR, and Insulated copper pipes
- Varying sizes to accommodate diverse system configurations and cooling capacities
- High-quality materials for durability and corrosion resistance
- Compatible with various refrigerants
- Range of fittings and accessories for seamless installations
- Customizable solutions to meet specific project requirements
- Backed by Finstar’s expertise in refrigeration solutions in Kenya.
Types of Refrigeration Copper Pipes
Our refrigeration copper pipes are available in different types and sizes to accommodate diverse system configurations and cooling capacities:
Hard Drawn Copper Pipes:
- Composition: Made from solid copper and are rigid and strong.
- Applications: Used in high-pressure applications, such as refrigeration and air conditioning systems.
- Advantages: Durable, resistant to corrosion, suitable for outdoor installations.
Soft Copper Pipes:
- Composition: Made from annealed copper and are more flexible than hard drawn pipes.
- Applications: Commonly used for connecting components in refrigeration systems, such as coils and compressors.
- Advantages: Easy to bend and shape by hand, ideal for tight spaces and complex installations.
- ACR Copper Pipes: Specifically designed for air conditioning and refrigeration systems, these pipes feature enhanced cleanliness and precise specifications to ensure optimal system performance.
- Insulated Copper Pipes: Pre-insulated copper pipes help minimize heat transfer and condensation, improving system efficiency and reducing energy consumption.
Sizes of Refrigeration Copper Pipes
Refrigeration copper pipes are available in various sizes, typically measured by their outer diameter (OD) in inches or millimeters. Common sizes include:
- 1/4 inch (6.35 mm)
- 3/8 inch (9.52 mm)
- 1/2 inch (12.7 mm)
- 5/8 inch (15.88 mm)
- 3/4 inch (19.05 mm)
- 1 inch (25.4 mm)
The choice of pipe size depends on factors such as the refrigeration system’s capacity, operating pressure, and flow requirements.
Installation of Refrigeration Copper Pipes
- Cutting: Use a pipe cutter to cut the copper pipe to the required length, ensuring clean, square cuts.
- Deburring: Remove any burrs or rough edges from the cut ends of the pipe using a deburring tool.
- Bending: Soft copper pipes can be bent and shaped by hand or with a tube bender to fit the layout of the system.
- Flaring: Use a flaring tool to create a flare at the end of the pipe for connection to fittings or components.
- Soldering: Join copper pipes and fittings using soldering or brazing techniques, ensuring leak-free connections.
- Support: Install pipe hangers or straps to support the copper pipes and prevent sagging or movement.
Maintenance of Refrigeration Copper Pipes
- Inspection: Regularly inspect copper pipes for signs of corrosion, leaks, or damage.
- Cleaning: Keep the pipes clean and free from debris to prevent clogs and maintain proper refrigerant flow.
- Protection: Apply insulation to copper pipes, particularly in outdoor or exposed installations, to prevent heat gain or loss and reduce condensation.
- Leak Detection: Use leak detection methods, such as bubble testing or electronic leak detectors, to identify and repair any leaks promptly.
- Corrosion Prevention: Implement corrosion prevention measures, such as using corrosion-resistant coatings or sacrificial anodes, to protect copper pipes from degradation.
Our refrigeration copper pipes are manufactured to the highest quality standards, ensuring durability, corrosion resistance, and compatibility with various refrigerants. We offer a range of fittings, joints, and accessories to facilitate seamless installations and provide customized solutions tailored to your specific project requirements.